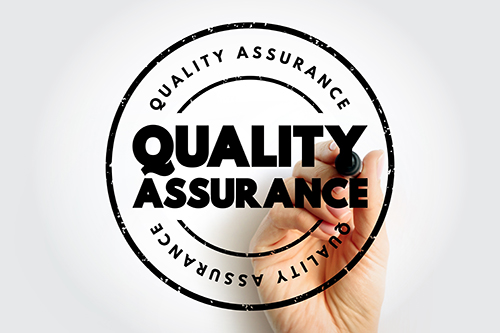
In manufacturing, quality assurance is the use of a quality management system that ensures consistency is maintained regarding the expected quality levels of the goods being produced. Quality assurance is sometimes confused with quality control. In reality, quality assurance is all about ensuring that each client receives quality products that don’t have any defects. Through quality assurance, a manufacturer can manage the quality of each product.
You have come to the right place for those wondering what is the difference between quality control and quality assurance. Quality control is a part of quality assurance, and it entails inspecting each product to ensure that it meets the required quality standards as expected by the manufacturer. Quality control involves walkthroughs, checkpoint reviews, and testing. Quality assurance entails all the proactive components of quality management, such as team training, defining processes, and educated tool selection. Auditing can also be a part of quality assurance. Generally, quality control is reactive and product-based, and quality assurance is process-based. Nonetheless, each component plays a major role in ensuring the quality management system is effective.
Why Quality Assurance is Important in Quality Assurance
There are numerous reasons why quality assurance is important in the manufacturing sector. The main reasons include:
- Cost Savings
Since quality assurance is a part of quality management, when done right, it can help prevent quality issues. This means that the manufacturer will not be tasked with returns, scrap parts, and byproducts arising from poor-quality items, and the manufacturer can save a significant sum of money in the process.
- Efficiency Boosts
Quality assurance ensures fewer defective products, which means the manufacturer can dedicate more resources, such as warehouse space, money, and time, towards creating more quality products or additional projects. It can take fewer resources to develop quality products if the processes put in place can support the success of such an initiative.
- Improved Customer Satisfaction
Customers normally receive better products within a shorter period, and there is an improved consistency level when a manufacturer uses effective quality assurance techniques. Since there is a low chance of defective products being produced, the consumers will witness a wide range of benefits and improved innovation and personalization since more resources are dedicated to handling some of these tasks.
- Time-Saving
When a system is set up, it usually takes time to detect errors. Nevertheless, correcting these errors will take longer when they aren’t controllable. When the right quality assurance methods are implemented, the main focus will be on actual development instead of spending significant time fixing errors. Before you create a product, first carry out quality checks. Failure to do so may seem fast; however, such a mistake can prove detrimental since you may waste time on rectifying mistakes and fixing errors.
- Helps in Winning the Trust of Customers
A customer is usually keen enough to associate with your business if you produce quality products. As a result, it is important to prioritize consistency and quality to satisfy your clientele. Implementing quality assurance shows that a business is concerned about its client base and their needs.
- Generating Good Revenue
Quality assurance is important since it ensures that a business won’t sell faulty products. The process of quality assurance is also important in ensuring that a business delivers good-quality products throughout. By ensuring that each product delivered aligns with the quality standards and specifications, a business can witness an increase in profit margins.
Ways on How to Improve Quality Assurance
By implementing quality assurance, it is possible to monitor the success of the production process and your business success. In the process, you can make the necessary changes; this way, the outcome of the customers and agents can improve. Some of the tips that can help in enhancing quality assurance include:
- Establish Clear Guidelines
A quality assurance program is supposed to have well-defined metrics and goals that will allow you to measure its impact on the business. Ensure the quality assurance aligns with your business objectives. Also, standards for agent-customer interactions should be established to ensure consistency.
- Monitoring Industry Developments
When you’re aware of industry developments and market trends, you can anticipate your client base’s changing needs and ensure they’re met on time. If you have access to interaction data, you can analyze it and determine whether the company has been failing and whether the current strategies need to be adjusted.
Conclusion
Although your business is witnessing increased sales, quality assurance is important in the long run. Through quality assurance, underlying factors linked to sales can be fueled, leading to improved aspects of your company. You can handle the whole process from one point of view with the right quality assurance platform. The right quality assurance platform can have a fully integrated learning management system, a customizable scorecard builder, and a reporting suite, making it possible to monitor the impact of the training on team performance and evaluate agents.