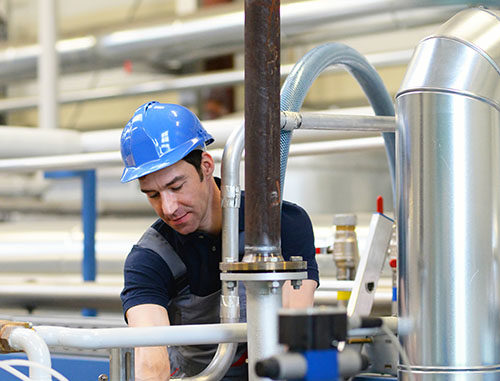
In today’s fast-paced industrial world, the efficiency of industrial plants plays a pivotal role in determining the productivity and profitability of businesses. However, despite advancements in technology and operational strategies, many industrial plants still grapple with common inefficiencies that significantly hamper their performance. These inefficiencies lead to increased operational costs and impact the operations’ overall environmental footprint, making sustainability harder to achieve.
Equipment Maintenance Downtime
Frequent equipment maintenance and the associated downtime emerge as major contributors to inefficiency within industrial plants. Proactive strategies like predictive maintenance, enabled by modern IoT sensors and AI algorithms, offer a powerful solution. These technologies predict failures before they happen by continuously monitoring equipment condition and performance, allowing for timely interventions that prevent lengthy downtimes. Upgrading to more reliable and easier-to-maintain machinery also plays a crucial role, as does training staff in effective maintenance practices. Implementing these solutions can significantly reduce downtime, boost productivity, and enhance the overall efficiency of industrial operations.
Energy Loss and Waste
Energy loss and waste are critical inefficiencies in many industrial plants, directly affecting operational costs and environmental sustainability. An active approach to mitigate these issues involves conducting regular energy audits to identify and address areas of significant energy loss. Investing in energy-efficient equipment and technology, such as LED lighting, high-efficiency motors, and advanced HVAC systems, drastically reduces energy consumption. Furthermore, implementing renewable energy sources like solar and wind power can provide sustainable alternatives to traditional energy supplies, significantly reducing carbon emissions.
Outdated Equipment and Software
Outdated equipment and software are major bottlenecks that undermine the performance and agility of industrial plants. Upgrading to cutting-edge technology platforms and machines that leverage the latest advancements in efficiency and productivity is the key to overcoming these challenges. Adopting smart factory concepts that integrate IoT devices, advanced analytics, and machine learning enables real-time monitoring and control of processes. These additions can also increase gearbox efficiency and the overall productivity of your manufacturing procedures!
Poor Inventory Management
Poor inventory management significantly undermines the operational efficiency of industrial plants. Excess inventory ties up capital and occupies valuable space, whereas insufficient stock leads to production delays and unsatisfied customers. Implementing an efficient inventory management system that utilizes the latest in RFID technology and supply chain analytics enables managers to maintain optimal inventory levels at all times. This strategy ensures materials are available when needed without overstocking, reducing storage costs and improving cash flow.
While modern industrial plants are the backbone of today’s global economy, their efficiency is often hampered by various common yet addressable inefficiencies. Recognizing and tackling these common inefficiencies in modern industrial plants is essential for enhancing productivity, reducing environmental impact, and ultimately achieving sustainable growth.