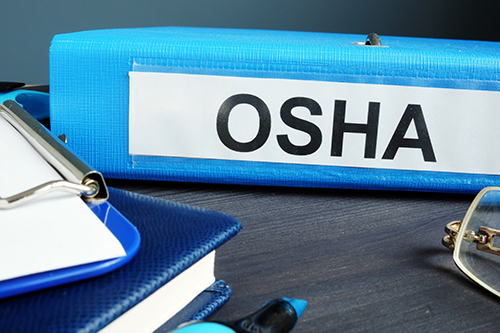
As an owner of a small industrial, manufacturing, pharmaceutical, or metal fabrication business, prioritizing the safety and well-being of your employees is crucial. Compliance with Occupational Safety and Health Administration (OSHA) regulations is a legal requirement and essential for maintaining a safe work environment.
A safe work environment ultimately saves you money. Safety inspections help prevent lost work hours due to injury, expensive and time-consuming worker’s compensation or medical claims, and damage to your business’s reputation that can deter workers and customers. Understanding the five most common OSHA violations and how to avoid them and taking proactive measures can help protect your employees and ensure your business avoids fines and costly shutdowns.
Fall Protection
Fall protection violations consistently top the list of OSHA violations across various industries. Conduct a thorough audit of your facility to identify areas where falls might occur to avoid fall-related accidents and potential violations. Implement safety measures such as guardrails, safety nets, and personal fall arrest systems to provide adequate protection for workers at elevated heights. Regular training and education on fall prevention are also essential.
Hazard Communication
Failure to comply with hazard communication standards is another frequent violation found in many industries. Having a comprehensive hazard communication program in place that includes proper labeling of hazardous materials, maintaining updated safety data sheets (SDS), and providing appropriate training to employees on the handling and use of hazardous substances is critical. Regularly review and update your hazard communication program to ensure compliance.
Respiratory Protection
OSHA frequently cites violations related to inadequate respiratory protection programs, including failing to conduct proper fit testing, providing improper respirators, or lacking a written respiratory protection plan. Assess the specific respiratory hazards in your workplace, select appropriate respirators, and establish a comprehensive respiratory protection program that includes training, fit testing, and regular equipment maintenance.
Lockout or Tagout
Lockout or tagout violations continue to be a concern, especially in manufacturing and industrial settings. Failing to properly control hazardous energy sources during equipment maintenance and servicing can lead to severe injuries or even fatalities. Develop and implement a lockout or tagout program that includes written procedures, employee training, and periodic audits to ensure compliance with OSHA standards.
Machine Guarding
Improper or inadequate machine guarding is a significant violation that poses serious risks to employees working with machinery. Injuries can range from amputations to fatal crush injuries. Machine guarding is important in all facilities that use powerful machinery, but is especially prominent in metal fabrication and manufacturing, or construction and packaging industries where cutting, bending, stamping, crushing, or grinding equipment is common.
Ensure all machinery and equipment have appropriate guards to prevent contact with moving parts, nip points, and other potential hazards. Conduct regular inspections and maintenance to identify and address any issues promptly.
You can create a safer work environment with reduced risk of accidents and injuries by taking proactive measures to address and avoid these five common OSHA violations. It is vital to establish a comprehensive safety program that includes risk assessment, training, equipment maintenance, and open lines of communication with employees regarding safety concerns.