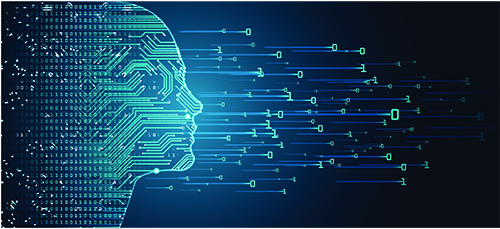
Popularized in 2015 at the World Economic Forum, the Fourth Industrial Revolution, or Industry 4.0, connotes the increasing use of interconnectivity and automation, including artificial intelligence (AI) and machine learning (ML). Industry 4.0 impacts global production and the manufacturing world which, in turn, affects the supply chain and the speed at which products or parts are created and moved along to the next step or to the end user. Integrated technologies employed in this revolution are bound to make even more of a profound impact in the near future as they continue to evolve and become even “smarter.”
The history of Industry 4.0
The use of steam and waterpower in the transition from hand production to machines by the mid-1800s in the United States and Europe marked the first Industrial Revolution. By the early 1900s, the installation of railroad and telegraph networks and increased electrification and phone service shortened the communication lag time and improved supply chain capabilities to usher in the second revolution. In the late 20th century, the rise of digital technology, coupled with the advances in computing power, led to the Third Industrial (or Technological) Revolution. The world is now in Industry 4.0, which the World Economic Forum labels as a “fundamental change in the way we live, work and relate to one another … enabled by extraordinary technology advances commensurate with those of [previous] industrial revolutions.” The increased use of AI, ML, and advanced robotics mesh the physical and digital worlds to make work and everyday life easier. It is also the driving force behind Industry 4.0.
Smart factories equal higher productivity
Employing AI and real-time big data analytics, coupled with the power of cloud computing and the Internet of Things (IoT), provides momentum as Industry 4.0 unfolds. The next step is to optimize automated and robotic manufacturing systems, which have already been in place for decades. AI is not a new concept but has reached another level as it gets “smarter.” The evolution of cyber-physical systems, which are a hybrid of digital, analog, physical, and human components, allows for increased productivity, scalability, improved metrics, and quality assurance.
Cloud computing technology enables large volumes of data to be processed more quickly, using algorithms to program a production line more efficiently. These technologies can flag potential problems with the equipment itself or a detected quality issue, for example, using sensors that employ a baseline and pre-programmed parameters. One example of this is 3D printing and additive manufacturing processes now can be held to tighter tolerances.
For manufacturing businesses where profit margins are often razor-thin, investing in the latest digital technologies that employ AI and ML may be what lands a company in the black. IoT and AI allow for greater flexibility, including the ability to remotely monitor and control an automated/robotic process. Real-time monitoring systems also can review data for possible safety and security concerns related to an automated manufacturing process—or for smart workplaces in other business sectors as well. Data collection from sensors located in automated or robotic systems that detect wear and tear can be used to institute predictive maintenance programs.
Big data and AI can keep track of supply chain issues and help keep the pipeline full, with faster data analysis, improved forecasting, optimized route planning for shipments, and even helping to select suppliers by analyzing the potential risks associated with a new vendor candidate based on business history. The further adoption of higher speed, higher bandwidth 5G technology will allow for critical data to be shared more quickly and used effectively, also making IoT devices operate more efficiently.
Using big data more effectively
Digital information analyzed post-production can be used to tweak processes and improve efficiency on the next run. AI can be harnessed to detect where bottlenecks are occurring in the manufacturing or shipping process and can analyze data for excessive scrap rates that may be present. If 100 assemblies move to a workstation but only 90 move on to the next operation (after an automated inspection routine, for example), AI can help flag that condition.
In some real-time environments, it may be better to use edge computing architecture, where local servers and connected devices, as opposed to a remote cloud server, can improve response times and minimize latency. It’s important to weigh the upfront investment costs and the derived benefits associated with setting up and servicing a local server farm compared to using a cloud-based system. Cloud computing is still employed to analyze the data collected and to make future improvements to the process via AI and ML.
It is often a costly and time-consuming process to learn new skills, hire and train the right people, and then invest in the latest digital technologies. This requires buy-in from the top levels of an organization and can be incentivized by the bottom line in the manufacturing world. As companies ponder this long-term strategy decision, they will need to consider if it will cost less to produce a part in the long run and whether it will be an improved part that may also offer a competitive advantage
The five pillars of Industry 4.0
Similar to the previous Industrial Revolutions that took several decades to be fully defined and evolved, the Fourth Industrial Revolution has not yet fully realized its true potential. The five pillars of today’s smart manufacturing environment are AI, 5G, IoT, big data, and the cloud, all of which can be adapted to fit a particular industry. With the continuing development of AI and ML and decisions on whether to fully employ cloud or edge computing methodologies on the factory floor, Industry 4.0 will continue to morph in the foreseeable future. For competitive and productivity reasons, many companies or business sectors that are holding out will now join the revolution and make the necessary upfront investment. The oil and gas industry is an example of a more traditional, legacy business sector that is waiting to see others take the plunge first. Those that don’t ultimately embrace Industry 4.0 risk being left behind.